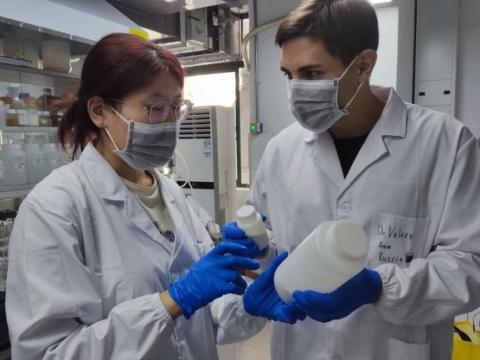
Высококачественный глинозем можно получать из золошлаков с помощью химических реактивов. Такую технологию разработали совместно ученые из России и Китая.
И такая разработка в теории может решить сразу две проблемы:
Проблему утилизации отходов угольных электростанций. В России накоплено уже примерно 1,5 миллиарда тонн золошлаков, и ежегодно к ним добавляется еще 25 миллионов тонн.
Проблему дорогого сырья для алюминиевых заводов. Российские заводы вынуждены импортировать глинозем, который за последнее время серьезно подорожал на биржевых рынках (с начала 2024 года цена на глинозем увеличилась практически вдвое, превысив отметку в $700 за тонну). В ноябре «Русал» сообщил, что сократит производство алюминия на 250 тысяч тонн на фоне резкого повышения цен на глинозем.
Глинозем — это оксид алюминия, он необходим для производства металлического алюминия. Ученые придумали способ удешевить производство сырье, при этом — без потери его качества. И использовать для этого можно золошлаковые отходы — побочный продукт сгорания угля на теплоэлектростанциях.
Разработкой технологии занимаются ученые из Института геохимии и аналитической химии имени В.И. Вернадского РАН (Москва), Уральского федерального университета (Екатеринбург) и Университета Тунцзи (Китай). Их работу поддержал Российский научный фонд (прочитать подробнее о проекте можно на сайте фонда). Сами результаты работы ученых опубликованы в Journal of Cleaner Production.
Чтобы получить из золошлаков глинозем, ученые использовали специальные реактивы. Отходы для исследования взяли с Рефтинской ГРЭС (Свердловская область, входит в СГК). Эта станция одна из крупнейших в России и лидер по отгрузкам золошлаков потребителям для переработки и последующего полезного использования. В золе Рефтинской ГРЭС содержится 25-27 мас.% оксида алюминия, что делает этот вид сырья весьма перспективным в качестве источника продукции для металлургии: карбида кремния — SiC и оксида алюминия – Al2O3 – глинозема.
Процесс преобразования золошлаков в глинозем в РНФ описывают так: золу в течение трех часов растворяют в смеси серной кислоты и бисульфата аммония при температуре 200°С. Затем полученный раствор охлаждают, и получаются алюмоаммонийные квасцы — это комплексная соль аммония, алюминия и серной кислоты. Ее очищают от примеси железа, растворяют в воде и осаждают в виде минерала алунита на поверхности затравки, которой служил минерал бемит.
Ученые меняли объемы используемых реактивов, температуру и длительность осаждения, чтобы определить, какие условия позволяют получить наибольшее количество алунита. На заключительных этапах синтеза алунит промыли аммиаком для удаления серы и обожгли в печи при 950°С. Максимальное количество алунита — промежуточного продукта синтеза — смогли получить в течение 8 часов при нагреве раствора до 90°С. Эффективность осаждения составила 88%.
Химический анализ подтвердил, что размер частиц и чистота глинозема, который получили ученые в результате работы, соответствуют требованиям государственных стандартов России, Китая и Индии. А значит, его можно использовать в производстве алюминия.
По словам Дмитрия Валеева, руководителя проекта, кандидата технических наук и введущего научного сотрудника лаборатории сорбционных методов ГЕОХИ РАН, главной инновацией предлагаемого способа стала возможность осаждения алюминия в виде алунита без использования дополнительных реагентов, например, газообразного аммиака.
«Использование бемита, а не традиционно используемого гиббсита в качестве затравки позволило снизить температуру кальцинации глинозема на 300°С. Таким образом, энергозатраты сокращаются на 30%.